متن کامل ساخت سکوهای دریایی را می توانید با کلیک بر روی عبارت ((ورق دریایی)) مشاهده نمایید.
_czjq.gif)
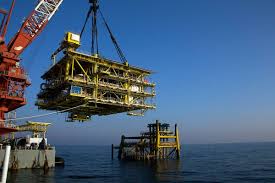
ساخت سکوهای دریایی
کلیات
منظور از ساخت در این مقاله، مراحل مربوط به مهیا سازی قطعات و ساخت قسمت های مختلف یک سکو در خشکی می باشد. ساخت سکوهای فلزی، شامل پیش ساخت و ساخت اجزا و زیر مجموعه ها می باشد. که از مراحل زیر تشکیل می شود.
1-بریدن قطعات
2-آماده کردن لبه های قطعات برای جوشکاری
3-زدودن زنگ زدگی از سطح فلز (سند بلاست یا گریت بلاست)
4-خم دادن و شکل دهی سرد یا گرم قطعات
5-گرم کردن قبل از جوشکاری
6-جوشکاری قطعات
7-زدودن اضافه های جوشکاری
8-سنگ زدن
9-عملیات حرارتی بعد از جوشکاری
10-مونتاژ زیر مجموعه ها برای ساخت مجموعه های اصلی نظیر جاکت و عرشه
11-قرار دادن و نصب تجهیزات تأسیسات
12-اعمال روشهای مناسب برای حفاظت در مقابل خوردگی
در این فصل مشخصات کلی و حداقل های لازم برای ساخت و مونتاژ پایه و عرشه سکوهای ثابت فولادی، ارایه می گردند.
برنامه ریزی
برای ساخت بهینه و اقتصادی یک سکوی دریایی، لازم است برنامه کار طراحی گردد. موارد مهمی که در این برنامه باید در نظر گرفته شوند، عبارتند از:
1-تقسیم مناسب سازه به اجزای مختلف، به گونه ای که ساخت این اجزا به صورت پیش ساخت ممکن گردد.
2-مشخص کردن ابعاد مختلف قطعاتی که به ناچار باید در محل کارگاه، تولید و به هم متصل گردند.
3-مشخص کردن محل های جوش
4-بررسی امکاان جوش، چه به صورت کلی و چه به صورت موضعی
5-فراهم کردن امکان حداکثر استفاده از جوشکاری اتوماتیک و پیوسته
6-بررسی سازگاری جوش دو قطعه فولاد با مشخصات فنی مختلف
7-در نظرگیری محدودیت عملیات حرارتی جوشهای قطعات در مرحله ساخت
ساخت سکوهای دریایی
برنامه مذکور باید در قالب مدرکی تحت عنوان روش ساخت توسط پیمانکار ساخت تهیه و ارایه بشود و مورد تأیید قرار گیرد. در این برنامه، تجهیزات و نیروی انسانی مورد نیاز جهت اجرای روش نیز باید مشخص شود.
مصالح مصرفی
کلیات
تمام فولاد سازه ای مصرفی باید، نو، عاری از نقص و زنگ زدگی باشد. در ضمن، استفاده از فولادهایی که از قبل برای مصارف دیگری رد می شوند. و سپس به عنوان فولاد سازه ای (فولاد ساختمانی) طبقه بندی می شوند، در سکوهای دریایی مجاز نیست.
گواهی کارخانه نورد
گواهی های اصلی آزمایشهای انجامی در هنگام تولید، باید بر اساس نیازمندی ها ارایه شود. این گواهیها باید تمام اطلاعات لازم در مورد مقاومت، شکل پذیری، چقرمگی، آنالیز شیمیایی، عملیات حرارتی. آزمایش های غیر تخریبی، آزمایش های تکمیلی و سابقه شناسایی تولید را در بر داشته باشد. قبل از استفاده از فولاد در ساخت سازه، گواهی های فوق باید ارائه شوند.
شناسایی مصالح
دریافت و جابه جایی مصالح، اغلب بخشی از فعالیت های پیمانکار ساخت است. پیمانکار باید روشی را جهت دریافت، انبار کردن، شناسایی و ردگیری ارایه داده و به تصویب برساند. در این روش، هر قطعه فولادی که در بخشی از سازه تولید بشود مورد استفاده قرار می گیرد. باید به صورت دقیق قابل ردگیری تا مرحله دریافت گواهی تولید کننده فولاد باشد.
انبار کردن مصالح
لازم است مصالح مورد مصرف برای ساخت در فضای مناسب بالاتر از سطح زمین، روی قطعات چوب، پالت و یا قطعات مشابه انبار گردد. طوری که مشکل خوردگی تدریجی وجود نداشته باشد. در این رابطه، بخصوص لبه هایی که برای جوشکاری بعدی مهیا می شوند. باید به طور مناسب حفاظت شوند و قبل از جوشکاری، مورد کنترل قرار گیرند تا اگر لازم باشد تمیز گردند. مصالح مصرفی برای جوشکاری، باید در شرایط خشک و زیر سقف نگهداری گردند.
جوشکاری
ساخت سکوهای دریایی
کلیات
برای اتصال قطعات و اجزای مختلف سکوهای فلزی، اغلب از جوش استفاده می شود. و به این خاطر، بررسی مشخصات مکانیکی و کیفیت آن بسیار مهم می باشد. جوشکاری مورد نیاز، باید به گونه ای انجام گیرد که کلیه مشخصات لازم و کیفیت مطلوب رعایت گردد. بررسی صلاحیت های مربوط به جوشکاری و مراحل جوش، باید مطابق با استاندارد جوش AWS D1-1 انجام گیرد.
رویه جوشکاری
رویه جوشکاری باید به صورت کتبی تهیه شود و در آن همه مراحل مختلف جوشکاری و متغیرهای مهم، مشخص گردند. در یک مدرک رویه جوشکاری، راجع به موارد زیر بحث می شود.
1-فرایند جوشکاری (نظیر جوشکاری دستی، جوشکاری اتوماتیک و غیره)
2-مشخصات مصالح و دامنه ضخامتی که آن رویه در مورد آنها قابل کاربرد است.
3-طراحی اتصالات (شکل قطعاتی که باید به هم متصل شوند، زاویه قطعات نسبت به هم، شکل نفوذ جوش و ریشه جوش و غیره)
4-نوع الکترودها
5-اندازه الکترودها و شماره و ترتیب پاسخ های جوش
6-جریان برق، ولتاژ و نرخ تغذیه الکترود
7-موقعیت های جوشکاری و جهت و سرعت حرکت جوش
8- گرم کردن قبل و پس از جوشکاری (روش، درجه حرارت، نرخ گرم یا سرد شدن و روش کنترل)
ساخت سکوهای دریایی
جهت کسب به شرایط بهینه جوش، باید آزمایش های متعدد انجام گیرد تا ضوابط لازم طراحی تأمین گردد. رویه جوشکاری باید منطبق بر استاندارد AWS D1-1 باشد.
فولاد رسول دلاکان
با سالها تجربه ارزشمند و گرانبها در عرصه تأمین و توزیع انواع ورق آلیاژی و انواع فولاد آلیاژی با گواهینامه ها و آنالیزهای معتبر با ضمیمه نمودن آن به محصولاتش آنرا به مشتریان خویش ارائه داده است. که توانسته رضایتمندی آنان را همواره فراهم آورد. صنعتگر شریف و گرامی از اینکه ما را جهت خرید کالا (فولاد آلیاژی) مورد نیاز خویش، انتخاب می نمایید از شما سپاسگزاریم.
ارتباط با ما
09122136675
02128423820
واتس آپ :09122136675
فکس: 02128423820
اینستاگرام :fooladdalakan
ایمیل: fooladrasuldalakan@gmail.com