متن کامل بررسی مودهای شکست لرزه ای را می توانید با کلیک بر روی عبارت ((مودهای شکست)) مشاهده نمایید.
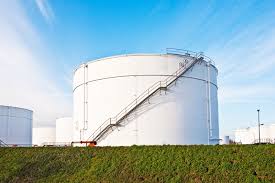
بررسی مودهای شکست لرزه ای و راهکارهای مقاوم سازی مخازن استوانه ای فولادی مهارنشده در یک مجتمع نفتی
چکیده
مخازن استوانه ای فولادی رو زمینی به طور وسیع در مجتمع های نفتی و از جمله انبارهای نفت ایران به کار گیری می شوند. تجربه زلزله های گذشته در کشورهای مختلف نظیر ژاپن، ایالات متحده، ترکیه و غیره نشان می دهد. که این گونه مخازن در مقابل حرکات نیرومند زمین در زلزله بسیار آسیب پذیر بوده. و مطالعات آسیب پذیری و مقاوم سازی آنها از اهمیت زیادی برخوردار است. در این مقاله رفتار لرزه ای 5 مخزن فولادی رو زمینی مهار نشده. در یک مجتمع نفتی با نسبت های ارتفاع به قطر (H/D) مختلف مورد مطالعه قرار گرفتند.
و انواع مودهای آسیب شامل کمانش پافیلی، کمانش الماسی. آسیب دیدگی سقف در اثر نوسان سیال، لغزش، واژگونی، بلندشدگی کف و نشست نامتقارن با تحلیل غیر خطی بررسی گردید. در این مطالعات، علاوه بر ارزیابی ضوابط آیین نامه های معتبر از جمله API650 و ASCE. تحلیل های استاتیکی، مودال، طیفی (خطی) و تاریخچه زمانی (غیر خطی) نیز بکارگیری شد. نتایج مطالعات موردی نشان می دهد که با در نظرگیری ارتفاع آزاد سیال داخل مخازن (free Board). برابر 13 درصد ارتفاع آنها، خطر آسیب دیدگی سقف از بین می رود. همچنین مخازن با نسبت ارتفاع به قطر بزرگتر و یا مساوی با یک (≤H/D) ناپایدار می باشند. سایر مودهای آسیب مذکور در مورد مخازن مورد مطالعه حاکم نمی باشند.
مقدمه یکی از انواع سازه های مهم که کاربرد فراوانی در پالایشگاه های نفتی دارد. مخازن فولادی رو زمینی نفتی هستند. که به شکل استوانه ای طراحی و اجرا می گردند. در واقع مخزن را وقتی رو میزی گویند که کف آن متکی بر بستر خاک یا پی باشد. یک مخزن فولادی از سه جزء اصلی تشکیل یافته است. بدنه، کف و سقف. کف مخزن ورق تختی می باشد که متکی بر بستر متراکم و یا شالوده گسترده بوده. و سقف آن نیز بسته به نوع ماده ذخیره شده به صورت ثابت و یا متحرک ساخته می شود.
بررسی مودهای شکست
مخازن رو زمینی نسبت به شرایط تکیه گاهی، به دو گروه تقسیم می شوند. مهار شده و مهار نشده. در یک مخزن مهار شده از حرکت قائم نسبی جداره در سطح پی جلوگیری شده است. در حالیکه یک مخزن مهار نشده در اثر تکان های شدید می تواند از روی زمین یا پی بلند شود. و بنابراین برای تحلیل دقیق دینامیکی آن آنالیز غیر خطی لازم است.
رفتار دینامیکی مخازن اولین بار توسط هاوزنر مدل سازی شد. و مبنای طرای آیین نامه ها قرار گرفت. وی چنین عنوان کرد که در یک مخزن دارای سطح آزاد که در معرض شتاب دینامیکی افقی قرار دارد. سیال از دو طریق بر روی جداره اثر می گذارد. 1) فشار نوسانی 2) فشار ضربانی. فشار نوسانی در اثرحرکت سیال مواج در بالای مخزن پدید می آید. و فشار ضربانی در اثر حرکت قسمتی از سیال در پایین مخزن و هماهنگ با پوسته ایجاد می گردد. فرکانس حرکت نوسانی به میزان قابل توجهی پایین تر از فرکانس حرکت ضربانی است. بدین معنی که این مود در پریودهای بالای زلزله تحریک می گردد.
در سال 2003 میلادی علی الزینی استاد و محقق دانشگاه کالیفرنیا. مقاله ای تحت عنوان ((بررسی پارامترهای مؤثر در پاسخ لرزه ای غیر خطی مخازن مهار نشده)) ارائه کرد. وی در این تحقیق اثراث فشار هیدرودینامیکی سیال را بر روی جداره مخازن مهار نشده در طول ارتعاشات ناشی از زلزله مورد بررسی قرار داد. و همچنین نتیجه گرفت که احداث مخازن بر روی فوندانسیون های انعطاف پذیر مناسب تر از اجرای آنها بر روی فوندانسیون های صلب می باشد. زیرا نرمی فوندانسیون سبب طولانی شدن پریود ارتعاشی مخازن در برابر نیروهای هیدرودینامیکی می گردد.
در سال 2004 میلادی نیز مارتین کولر به همراه پراوین مالهوترا مقاله ای تحت عنوان ((ارزیابی لرز های مخازن مهار نشده)) ارائه نمودند. که درآن هفت مخزن با نسبت های ارتفاع به شعاع مختلف (H/R) تحت بررسی قرار گرفت. آنها چنین عنوان کردند که یک ارتباط تنگاتنگ بین نسبت (H/R) و بلندشدگی کف مخازن وجود دارد.
مطالعات آسیب پذیری لرز ه ای مخازن فولادی موجود در یک مجتمع پالایشگاهی در سال 2006 نشان داد. که حدود 40 درصد مخازن موجود بسیار آسیب پذیر بوده و نیازمند مقاوم سازی اساسی هستند.
در این تحقیق، 5 مخزن موجود در یک مجتمع پالایشگاهی با نسبت های ارتفاع به قطر مختلف مورد ارزیابی قرار گرفت. علاوه بر کنترل ضوابط آیین نامه ای تحلیل های استاتیکی، مودال، طیفی و تاریخچه زمانی غیر خطی برای هریک از مخازن صورت پذیرفت.
مودهای آسیب مخازن
آسیب های وارده به مخازن را می توان در قالب هفت معیار آسیب پذیری بیان نمود. که به صورت مختصر عبارتند از:
واژگونی
وقتی نسبت ارتفاع به قطر زیاد می شود. پایداری مخزن در برابر این آسیب دیدگی کاهش می یابد. علت این پدیده بالا رفتن ارتفاع مرکز ثقل مخزن می باشد. این معیار با استفاده از ضوابط آیین نامه API650 و بر اساس نسبت M[D2(WL+Wt)] کنترل می گردد. در این رابطه M لنگر واژگونی مخزن بر حسب (N/m) و WL وزن محتویات مخزن. و در واحد طول محیط (N/m) و Wt وزن ورق جداره در واحد طول محیط مخزن بر حسب (N/m) می باشند. در صورتی که این نسبت بیشتر از 1/57 باشد مخزن ناپایدار بوده و واژگون خواهد شد.
کمانش الماسی جداره
تنش های فشاری که ایجاد شد در جداره مخازن سبب بروز کمانش در قسمت های میانی آن می گردد. که کمانش الماسی (کمانش الاستیک) نام دارد. مخازن با ارتفاع زیاد معمولاً دچار چنین آسیبی می شوند. این آسیب با محدود کردن تنش فشاری ایجاد شده. در جداره مخزن و مقایسه آن با تنش مجاز جداره مطابق با ضوابط آیین نامه api650 کنترل می گردد.
کمانش پافیلی جداره
کمانش پافیلی (کمانشی الاستوپلاستیک) معمولاً در مخازن بزرگ و در ارتفاع 1/5 تا 2/5 متری از کف مخزن رخ می دهد. علت ایجاد چنین کمانشی آن است که در هنگام بلند شدن قسمتی از کف مخزن تحت اثر نیروهای جانبی زلزله. در طرف مقابل آن تنش فشاری قائم به شدت جلوگیری از افزایش می یابد. در این حالت ترکیب دو تنش کششی حلقوی و فشاری قائم باعث ایجاد این کمانش در جداره می گردد. بدین ترتیب جلوگیری از افزایش بیش از حد تنش کششی حلقوی در جداره مخزن معیاری برای کنترل کمانش پافیلی محسوب می شود.
فولاد رسول دلاکان
با سالها تجربه ارزشمند و گرانبها در عرصه تأمین و توزیع انواع ورق آلیاژی و انواع فولاد آلیاژی با گواهینامه ها و آنالیزهای معتبر با ضمیمه نمودن آن به محصولاتش آنرا به مشتریان خویش ارائه داده است. که توانسته رضایتمندی آنان را همواره فراهم آورد. صنعتگر شریف و گرامی از اینکه ما را جهت خرید کالا (فولاد آلیاژی) مورد نیاز خویش، انتخاب می نمایید از شما سپاسگزاریم.
ارتباط با ما
09122136675
02128423820
واتس آپ :09122136675
فکس: 02128423820
اینستاگرام :fooladdalakan
ایمیل: fooladrasuldalakan@gmail.com